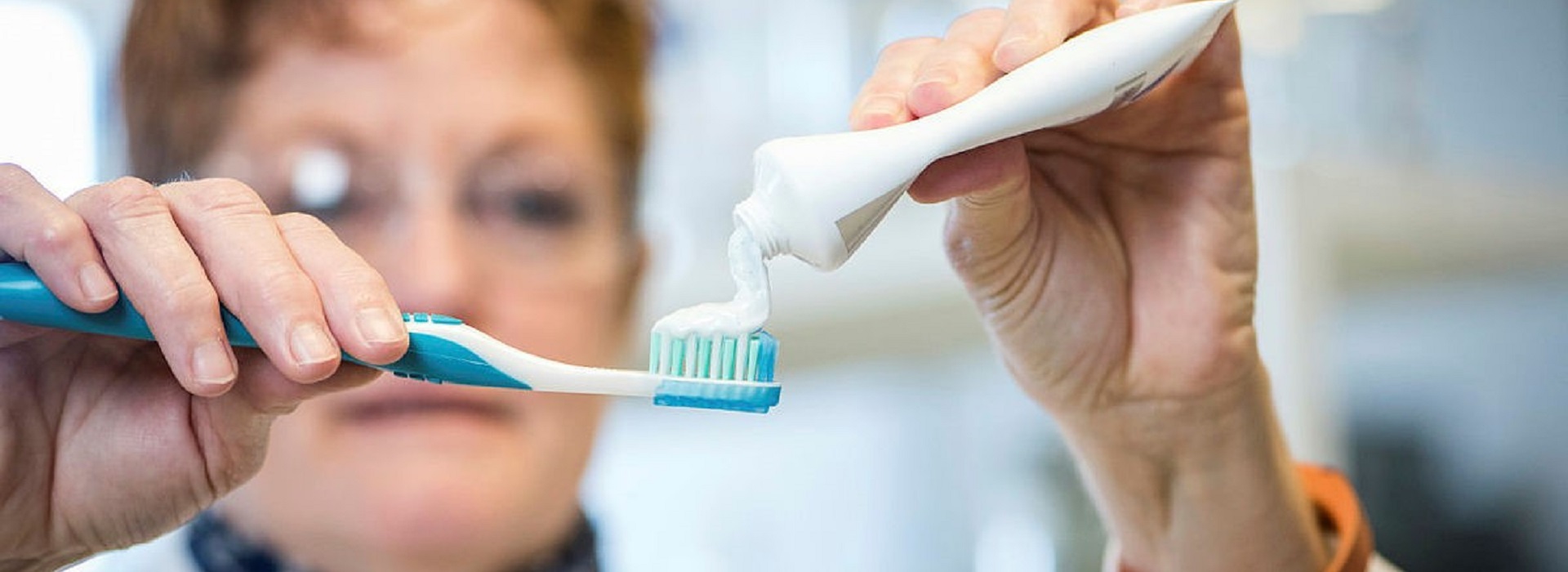
Naturbeads – sustainable microbeads replace microplastics in cosmetics & toiletries
Naturbeads – biodegradable cellulose microparticles to replace plastic microbeads
Naturbeads is a spin-off company that started at the University of Bath, thanks to the interdisciplinary work of two researchers with an interest in replacing plastic microbeads and the dedication of a CSCT PhD student.
Since it was founded in 2018, Naturbeads has already received many prizes for their innovative technology plus further funding through the Plastic Research and Innovation Fund, a partnership between UK Research and Innovation (UKRI) and Sky Ocean Ventures (SOV).
Plastic microbeads – useful, versatile, but unsustainable
The concerns posed by the use of plastic microbeads has long been recognised by experts. Their small size, extreme durability and widespread usage results in leakage of these microplastics into the environment, where they rapidly accumulate and lead to detrimental effects – not only for wildlife but also for people as they enter the human food chain.
Plastic microbeads serve diverse functions in a wide range of products: they can be used as an abrasive or exfoliating agent; they add a silky, spreadable texture to lotions; they are used in biomedical research techniques; and they create porousness in materials like ceramics. Significant research and development is ongoing to find replacement materials that can fulfil many of the same functions but that are also biodegradable. However, the very properties of plastic microbeads – durability, low cost, inertness, ease of manufacturing – make their replacement challenging.
The consumer products and cosmetic industries were the first to start searching for sustainable alternatives, pushed by the public’s desire for natural materials and growing awareness about plastic pollution. Although some potential alternatives were identified, none met all the necessary criteria. For example, silica is natural and hard, but not biodegradable; PHAs can be made into spheres but are expensive and cannot meet mechanical and optical requirements for most applications; and crushed shells are cheap and biodegradable, but cannot be made in spherical form.
Long requirement lists for the material itself, coupled with significant regulatory burdens for any products that enter the human body, have pushed some companies to eliminate beads altogether while a viable solution is found.
Sustainable science meets sustainable engineering
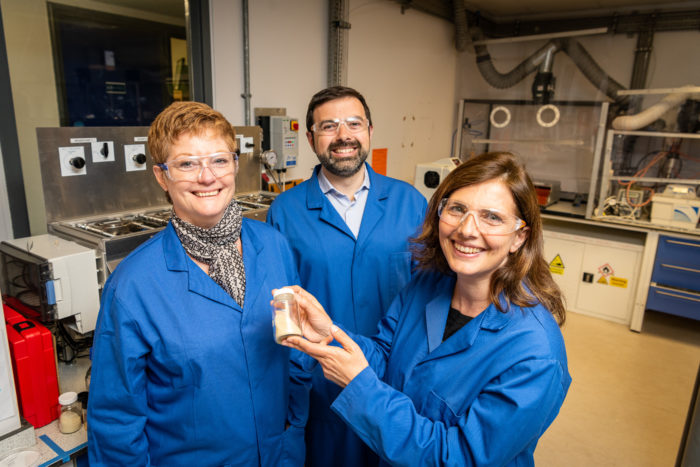
From left to right: Professor Janet Sott, Professor Davide Mattia and Dr Giovanna Laudisio
Back in 2011, the late Janet Scott, Professor of Sustainable Chemistry, and Davide Mattia, Professor of Chemical Engineering, University of Bath, started developing a new concept to replace plastic microbeads using cellulose. The idea was born while they worked on a TSB Innovation Grant to develop metal-free carbon particles, and it was solidified through their involvement with the Centre for Sustainable and Circular Technologies (CSCT).
“Cellulose is what plants are made of. It’s an incredibly abundant, natural material. It’s renewable and biodegradable, and it isn’t fossil-fuel derived. However, it is also a very stable material – which is a good thing as, otherwise, trees would melt away every time it rained, but a huge challenge when it comes to dissolving it to process it”, says Davide.
The first challenge Janet and Davide encountered was identifying the right solvents and type of process needed to dissolve cellulose for the purpose of creating microbeads. After that, they had to develop a technology that could potentially be industrially scaled.
“With the CSCT’s Centre for Doctoral Training in Sustainable Chemical Technologies, Janet and I were able to secure a PhD student, James Coombs-O’Brien, to develop this concept. With James, we put together the chemistry needed to dissolve cellulose and worked on finding the suitable solvents for a continuous (production) process using membranes”, said Davide. “This was the bulk of James’s PhD, and it resulted in a publication that came out in 2017, before the UK enacted a partial ban on the use of plastic microbeads in rinse-off cosmetics.” This, plus further recommendations by the European Chemicals Agency to extend restrictions to all types of plastics microbeads in every application, spurred industry to find sustainable alternatives to meet the new regulations.
Following James’s publication and enactment of the ban, the research team started receiving sample requests that quickly evolved into much larger orders – 100kg, 2 tonnes – that could not be processed at the University. After receiving many of these calls, the team decided to address the issue. Using funding secured from the Impact Acceleration Account (IAA) at the University*, they were able to recruit Dr Giovanna Laudisio to analyse the market to understand demand for this product and industry needs and constraints. The results were encouraging, so Davide, Janet and Giovanna founded Naturbeads in May 2018.
From proof-of-concept to spinoff
The next step for the team was attracting funding to develop the technology. Sky Ocean Ventures, an impact investment vehicle offering venture funding to help companies develop technologies to reduce plastic pollution in the ocean, had recently made an agreement with Innovate UK to fund ten UK-based companies with promising solutions. The Naturbeads team submitted a proposal and received the funds to start operating in May 2019.
Following the grant, Naturbeads issued an industrial contract to the University of Bath, whereby the company is currently hosted in the University labs. Janet and Davide took a role as Technical Advisors for the company, while Giovanna was appointed CEO. They hired a technician to work in a small, lab-scale rig developed to produce samples for cosmetic companies, so they can test if the material works for their formulations; and also recruited a process engineer to design and build a pilot plant for larger-scale production.
“Naturbeads’ mission is not to become a bead manufacturer, but to develop a technology, a manufacturing solution, equipment, software, know-how and IP for ingredient manufacturers to adopt when making their beads to sell to cosmetic companies.”
“This project was only ever made possible through the CSCT’s concept, which enabled us to combine Janet’s knowledge in biopolymers and my expertise in membranes and process engineering to develop a novel product. Without either component, this would have not been possible, because we needed to compatibilise the chemistry and the solvents with the process, and vice versa. This is really where working together, chemists and chemical engineers, we can deliver a significant improvement over what they can do individually. The CSCT students represent a very good route for academics to collaborate, while also allowing the students to learn and develop new knowledge. This is a very good incentive to work together and to start fantastic collaborations like the one that led to the founding of Naturbeads.” – Davide Mattia.
“Scaling up a technology from TRL 3/4 to TRL 6/7 is the most challenging part of the innovation process, so much so it is also known as ‘the valley of death’. Without the right support, many interesting inventions from academic research would not reach commercialization, because big corporations are risk-averse and prefer to wait that the technology has reached a higher maturity level. For this reason, Naturbeads is grateful for the support received by the University of Bath and the Department of Chemical Engineering which is hosting us. The access to top-class facilities and the know-how developed in many years of research are the right ingredients to support a young startup and increase our chances to successfully scale up the technology to produce cellulose beads which continues to raise a lot of interest from the market and from investors.” – Giovanna Laudisio.
Dr James Coombs-Obrien went on to work at Dyson’s car division. Building upon the knowledge developed in cellulose beads, Davide, Janet and Professor Karen Edler (another CSCT academic working in the Department of Chemistry) have secured further EPSRC funding for Biobeads, a research project focused on the development of sustainable capsules used, for example, in washing liquid to contain detergent or perfume, as these are currently also made of plastic.
In 2020, Naturbeads has been awarded £47,000 by Innovate UK for a three-month project as part of the competitive Small Business Research Initiative which enables organisations to research and develop products that provide innovative solutions. This is the 3rd Innovate UK grant awarded to the company since January 2019, having received a total amount of over £1m.
*This project was funded through the Engineering and Physical Sciences Research Council (EPSRC) via an Impact Acceleration Account (IAA), an institutional grant to the University of Bath (Grant Ref: EP/R51164X/1) and managed by the CSCT.
STBAH is partnered with the University of Bath and the business incubator SETsquared.